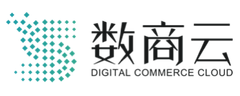
工业互联网最早诞生于2012年的美国。在移动互联网和消费互联网风起云涌之时,工业互联网并不为人所关注。
近年来,三一重工、海尔、华为等大型企业,阿里、腾讯等互联网巨头都纷纷布局工业互联网。2020年4月,国家发改委明确“新基建”范围,工业互联网也位列其中,作为重要组成部分之一。
中国现在为什么迫切需要工业互联网?
工业互联网会如何落地?将如何满足中国智造的真实需求?
工业互联网并不是一个新概念,GE在2012年就已经提出。为什么时隔八年,国家层面提出要大力建设工业互联网?这里面的底层逻辑是什么?
高世太:中国现在拥有全世界独一无二的全产业链的工业体系,全世界最为高效的物流/人流网络。
但同时可提升的空间还比较大,在高附加值产品和服务的环节还相对比较薄弱;生产规模大但生产效率不高;在需求端快速变化的同时,供给端不能做到同样的灵活。
中国工业面临着如何提升产品附加值、提升生产效率、更好的匹配供需关系等问题。这就要求工业体系在完善的商品流、物流的基础上,在数据流层面完成一次系统升级,将整个工业体系全面智能化,以更好地匹配和适应供给和需求两侧的变化。
要编织出来整个工业体系的这张“数据的网”,且全面实现智能化,工业互联网必不可少,这就是国家提出建设工业互联网的底层逻辑。
但是强调一下,今天所有的讨论都是基于中国。中国目前的全产业链,发达的交通基础设施和物流网络,所以中国的工业互联网发展不同于别的国家,无论从路径还是速度。
高世太:现在中美产业链解耦的趋势已经越来越明显。中美的关系日趋紧张,无论是华为事件还是近期的领事馆关闭,都是这方面的体现。
面对这种情况,中国工业体系需要做的是,在全产业链的层面提高效率,让“全球产业链剥离中国”这个动作变得在成本上不可承受,同时在底层技术、核心零部件等领域完成全面的国产替代,这需要借助工业互联网。
同时,无论欧美市场是否对我们关上大门,我们都需要扩大内需。扩大内需意味着我们的工业体系要能生产高端产品,要更快、更灵活的生产,这也需要工业互联网。
从消费者需求角度来看,以直播带货为代表的新模式、新渠道的崛起,将给生产端带来什么样的变化?会加速工业互联网的落地么?
高世太:新模式、新渠道的崛起,标志着个性化消费的崛起。个性化消费需要更高效、更灵活的供给端。
传统的供给端习惯的是标品生产,转产慢且成本高;新兴的需求端要的是个性化,变化快。
也就是说,需求端的变化对供给端提出了更高的要求,但目前供给端没有跟上。需求端和供给端的这种不匹配造成了供需关系结构性失衡,中低端产品过剩,但高端产品不足,难以满足快速变化和升级的需求。
如果从更高维度看,消费互联网已经将我们每个人的需求充分数字化、线上化,但生产端还是用老师傅的方式生产,数字化程度低,造成生产端和需求端的数字化程度不匹配。
要解决这些问题,需要工业互联网来为中国的工业体系赋能,对供给端进行数字化改造,让整个工业环节的数据流动起来,与需求端形成有效映射,及时洞察和响应需求端的变化。
能不能用一句话来概括,工业互联网如何赋能中国工业体系?
高世太:数据驱动智造。
所谓“数据流动层面实现升级”,数据流动指的是什么?
高世太:一个典型的工业企业,一般分为产品设计、工艺设计、生产制造、产品测试、运维等阶段,一个产品从原材料到生产出来交付到消费者手中大大小小需要经历三十个左右的关键环节。
以工厂为例,在数据流动层面实现升级意味着生产各环节数据互通,让数据流动起来,而不是一个个数据孤岛。
高世太:从统计数据可以看到,只有约45%的企业实现了产品设计与工艺设计之间的数据打通;只有约三分之一的企业实现了产品设计、工艺设计、生产制造之间的数据打通;而只有不到20%的企业能实现产品全生命周期的数据互通。
高世太:首先工业环境是比较复杂的,一条生产线上可能会用到各种各样的设备,这些设备之间都不是互联互通的。这些工业现场里面的设备我们一般称之为OT层,区别于手机、个人电脑这样的IT端。
复杂到什么程度呢?全世界有超过100种工业总线,各类终端设备的通讯协议大概有4000-5000种,负责工业数据的采集、解析和转换的驱动有5000余种,包括PLC、变频器、板卡、智能模块、智能仪表、标准协议、机器人、机床等。
如果只是实现产品设计与工艺设计之间的数据打通,主要需要IT层面的融合;实现产品设计、工艺设计、生产制造之间的数据打通则需要IT层和OT层的融合。
实现产品全生命周期的数据互通不仅需要IT层和OT层的融合,还需要OT层之间的融合,打通OT层的各个数据孤岛,实现工厂内部各环节的数据和市场营销、售后支持、维修、客服这些环节的数据全面融合。这对人才、资金和技术都提出了很大挑战。
这种现状是否意味提升空间其实很大?
高世太:基于中国工业的体量,每个细分行业都是千亿级的,都值得花时间去研究,去探究到底它应该怎么去做数字化转型。
除了行业维度,还可以从工艺维度看。不同的行业可能都需要相同的工艺环节,比如说做机加工的,或者是做模具注塑的,或者电子产品制造里面很多要做PCB和SMT贴片的。
从这两个维度去看,数据化的提升空间巨大。
从更好的获取高质量数据的角度蓝驰已经做了一些底层核心要素的布局。蓝驰投资了一家做RISC-V架构和AIoT生态的公司。
与此前的ARM架构相比,RISC-V架构是一个开源的架构,是一个可以灵活根据应用场景去定义芯片的架构。
用户可以在不懂芯片的情况下,快速的去定制出来符合自身细分场景所需要的传感器和芯片,进而把这种细分场景的核心数据收集上来,同时做到低成本低功耗等优势,让获取高质量数据的门槛大大降低;在此基础之上做数据化和智能化,再基于这两个核心要素实现行业整体解决方案去改造这个行业。
高世太:如果一家工厂实现了全流程数据互通,在每一个环节都可以有效率的提升,指数级的提高整体效率。如果做到一个比较理想状态的话,就是数字孪生,也就是不用实际生产出来,工厂就知道这个产品的质量如何,良品率如何,会不会卖的好等等。
如果将来工业互联网大规模落地的话,不仅是一家工厂内部的全流程数据互通,而是整个产业链的全流程数据互通和数字孪生。
再举一个电力行业场景的案例,我们国家这些年来在创造着一个接一个的电力奇迹,截至2018年的发电量统计,中国以8.4%的迅猛增速领跑全球,全年发电量达到71118亿千瓦时,几乎是以“一己之力”,生产了全球超过1/4的电量,为14亿人口和庞大的工业体系提供强有力的支撑,我们国家有绵延数万公里的输电线路,其中挑战比较大的环节,就是输电。
一家全自动无人机场超低空一体化解决方案的公司,解决方案之一是为输电线路提供巡检支持,它的无人机是没有人类飞手的,用AI算法自动规划自家巡检路径并不断优化。如果有飞手,每个人飞出来的轨迹都是不一样的,很难做到数据化。这家公司的无人机和无人机场解决方案把巡检线路,输电线路上的各种故障全面数据化,还对超低空的整个空间(200米以下)做了3D数据化,不仅巡检效率有了指数级提升,未来还可以根据数据预测故障的发生率,让输电公司提前做检修。
高世太:举一个调研过的模具和注塑厂的例子,生产各种各样塑料包装的,比如饮料的瓶子,化妆品的瓶子等。
日常生活中的一些快消品,比如酱油、饮料瓶上面有一个非常难做的东西,就是那种有拉环的瓶盖。为什么难做?因为需要让客户一拉就可以拉开,不能拉半天拉不开,也不能很松,一拉就坏掉了。
这看似简单,但实际是一个技术含量很高的生产工艺。而这些都是通过注塑设备生产加工出来的,而在注塑之前,需要先制造用来生产这种产品的模具。
模具被称为工业之母,中国的模具生产体量占了全球超过三分之一的规模,体量巨大。
现在的模具生产主要靠人工,效率低而且很难沉淀生产数据;以前的情况是大部分工厂只需要生产标准化的瓶盖或者塑料产品就可以,现在因为消费升级带来的需求端的变化,需要各种包装产品的多样化和个性化,传导到生产端后,就要求工厂能生产越来越多不同形状,不同规格的瓶盖和包装,而且要求整体的交期越来越短。
这对生产效率和工艺有很高要求,同时还要保证质量,这对生产端来说是一个双重挑战。
我们投资的一家企业,可以帮助这类的模具和注塑生产厂实现数据化,用新型的技术把模具生产中每一种不同的工艺,不同的材料,以及生产设备本身的情况数据化,实现快速且灵活的生产,同时在数据化后赋予智能化,让工厂可以更快更好地生产出来以前生产不出来的高质量产品,进而实现专业化的分工,利用这种数据积累,让不同领域的模具注塑厂商生产专业的产品,不再同质化,可以想象将给这个传统行业带来巨大的变革。
需要特别注意的是,对于工厂来说,能不能实现数据化,进而做到快速生产、灵活生产,现在已经不是一个能不能活得更好的问题,而是一个生死问题。
现在的需求方对时间的要求很高,比如同样数量同样规格的一批货,之前线下零售那样的渠道要求两到三个月内发货,现在直播带货这样的新渠道要求15天内发货,你如果15天内发不了货这笔订单就丢了,所以工厂需要想尽办法在每个环节提升效率。
还是以注塑厂使用的这个解决方案为例,原来一组瓶盖需要60秒,现在引入了更加数据化和智能的手段后,只要40秒就完成了,工艺和效率提升所赢得的时间周期,为企业提升了很大的获取订单的竞争力。
提升总体效率的好处,不仅体现在生产单一产品需要的时间更短了,还意味着生产更加灵活,可以满足个性化需求和快速转产。
还是刚才的例子,单个成品的出产时间缩短后,机器就有时间去生产批量个性化的订单,比如生产不同规格和要求的瓶盖。
单一环节效率提升,和柔性生产的能力是相辅相成的。
工业互联网创业者和消费互联网创业者的差异是?
高世太:首先需要创业者转变思维模式,与此前消费互联网有较大的区别。不管创业者之前的背景如何,要从之前的“从数据出发”的探索模式,转变到“从问题出发”的工程模式。
工业场景离日常生活相对较远,工业互联网企业要深入场景,了解工厂的真实需求和痛点。
工厂经营者是非常现实的买方,创业者的解决方案要能说的清楚价值,快速形成价值闭环,显得至关重要。
工业场景的智能化&数字化转型要用“小数据+小任务”的模式,在“小场景”下形成“小闭环”,实现单元智能;多个单元智能之间的数据融合,形成集群智能;多个多元集群智能之间的数据融合,形成系统智能。
什么是“从问题出发”的工程模式,如何深入场景?能举个例子吗?
高世太:举一个纺织项目的例子。纺织行业在制造端大概分纺纱,织布,印染,成衣这几大环节,其中在印染这个环节企业有较大的痛点,要解决的是“一次染色成功率不高“这个问题。
印染这个环节要用到染缸。染缸里面有物理变化,有化学变化,还有光学的一些因素,要配合很多注剂。
以前是靠老师傅,凭着感觉和经验去印染,不同的老师傅操作手法不同,且这种感觉和经验只能靠手口相传,很难准确的教会其他人。
所以,纺织工厂都会关注一个指标:印染的一次成功率。因为如果印染的一次成功率提升1%,工厂可以降低10%的成本。
创业者要做的,是把染缸里的物理变化,化学变化,光学反应,各种试剂成分等尽可能地数字化,形成针对印染这一环节,可以提高印染一次成功率的行业解决方案。这需要创业者有很强的行业know-how,真正的深入场景,发现痛点。
工业互联网的核心并不在于联网,我们观察到不少的产品确实是能把设备都连起来,但连起来以后到底能做什么其实是没有想清楚的。
归根结底,还是没有理解这个行业,或者是没有理解这个行业本身的痛点是什么。
高世太:没有标准答案。每个行业都不一样,每个行业数字化转型的路径也不一样。还是需要回到刚才说的,创业者要深入场景,发现痛点。
举一个例子,做行业解决方案和做平台这两种路径哪个更好?首先,不是每个行业都有做平台的机会,甚至有些行业的某个环节都没有做平台的机会,一定要看具体行业具体环节。
再举一个例子,如果创业者要做平台,要选择什么样的路径?比如刚才做模具注塑的例子,首先通过提高数字化和智能化的方式,帮助这个行业提升了工艺水平,能够更快更好地做出原来做不出来的产品,然后再去实现行业的专业化分工,进而实现行业分布式智造平台的可能。
创业者要发现一个行业最本质的痛点,用解决痛点的方式形成核心抓手,在每个环节去做好数字化的改造。
当数字化的改造做到一定程度之后,双边就有了产生平台的土壤,而不是还没有搞清楚行业的痛点和可以提升的空间,一上来就试图通过流量聚集的方式搭建一个平台。
高世太:其中一个维度是按纵向领域分,首先我们关注底层核心要素,包括芯片,工业软件,工业安全、核心零部件等。
在这些方面蓝驰已经有了一些布局。工业软件比如设计仿真,产品生命周期管理等软件我们都会关注。
另外从行业和工艺环节维度,我们会关注第二产业的各个细分行业的解决方案,流程制造行业偏上游,化工,能源,电力都是很大的行业,离散制造行业离消费者更近些,如汽车,3C电子,家居,机械加工,模具注塑等,每个细分行业和大的工艺环节都是近千亿的规模,有很大的空间。
但是数据化和智能是关键,抓住了这两个核心要素,才能获得改造这个行业和商业模式延展的可能。
文章来源:蓝驰创投;
【数商云www.shushangyun.com】致力于提供企业级的电商平台服务,长期为大中型企业打造数据化、商业化、智能化的网上商城系统解决方案,同时我们还提供B2B电子商务网站、B2B2C多用户商城系统、B2C电子商务系统、跨境进口电商平台系统、srm供应商管理系统、渠道商管理系统、B2B订货管理系统、采购商城管理系统、直播系统、新零售平台等一系列系统定制开发服务。